11-18 断裂失效是指金属、合金材料、机械产品的一个具有有限面积的几何表面的分离过程。断裂是发动机曲轴在运行过程中的主要失效形式,且疲劳断裂居首位,占失效实例约60%,对企业生产和经营造成巨大浪费和损失,那么曲轴断裂失效分析特别重要,可以防止同类失效现象的重复发生,为改进设计及加工工艺提供依据,消除隐患确保产品安全可靠等,同时也是企业节能增效的有利途径。+ C. Y) A n; ]; u. F; l
: Q& W" _7 b/ m/ [5 g2 [) Z' l ?2 r+ r3 N0 l5 }( z6 ~
一、曲轴断裂简介4 T0 v' M8 I& f2 ~7 W2 y
曲轴作为发动机核心零件之一,由于加工基准在曲轴中心孔和主轴颈间经常转换,产生基准不重合误差,再加上各轴颈加工精度高和轴类零件加工过程中刚性差的特点,是发动机本体五大件中加工质量最难保证的零件。同时,曲轴又是把燃烧气体推动活塞进行直线运动转变成回转运动的桥梁,曲轴的旋转运动是整车或发动机的动力源,因此曲轴的寿命是发动机考核的关键指标之一。由于曲轴在工作中承受交变载荷,主轴颈和连杆颈圆角过渡处属于曲轴强度的薄弱环节,长期的高速旋转运转和较大的交变负荷应力将造成曲轴圆角处产生裂纹或断裂。轴颈圆角处、轴颈表面如有缺陷,将成为裂纹源,易造成曲轴的早期非疲劳断裂。裂纹源一般位于连杆颈R角处,沿着约45°方向往曲柄梢扩展,最后断裂,包括裂纹源、裂纹扩展、断裂三阶段。如图1、图2所示。
. ]6 ~: m4 B$ u6 u0 J5 e: s
a" r+ o; j- S0 L 曲轴的断裂大多是突然发生,易引起人员的伤亡和机器的损坏,造成的损失非常巨大,是曲轴生产厂家生产经营中特别关注的课题。# k8 j" w2 A. j% d# P5 F. K1 h4 x
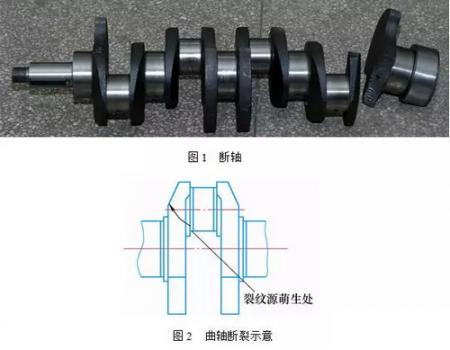
4 @; s3 l1 M, I$ r" T% a! z" m 6 J6 T8 a) ~2 R- J j$ {& w7 |
# j: T. Q/ W0 Z0 C, |: {二、曲轴断裂分析* H5 p) M" [9 m. g4 |0 b: E$ j' j
曲轴断裂的原因主要有以下几种情况:
$ N* `; O. N4 C0 J6 x1.机加工不符合要求
- ~ R" j, z5 z: H(1)曲轴制造质量不好,加工粗糙、材质不佳,达不到设计要求。
9 k- G3 G7 V7 |1 B1 x6 n(2)各缸工作不平衡,活塞连杆组重量偏差过大,引起曲轴受力不均而导致断裂。
6 L/ V1 K, L3 N* K4 o* @' e(3)冷校直也是曲轴断裂的一个原因。因为校直是塑性变形,会产生微裂纹,大大降低了曲轴的强度,因而在交变载荷的作用下,会导致曲轴断裂。
2 b9 _) _$ M' a3 M" |(4)各道主轴承中心线不同心,使曲轴受交变压力的作用,导致曲轴断裂。造成主轴承不同心的原因,除了缸体热处理过程中自然失效机体本身变形引起的以外,往往还由于维修装配或刮瓦时主轴承不同心引起。- X& A; q. }) Y1 _, f# ], c# G
(5)曲轴轴心线偏移使飞轮偏摆,在惯性力的作用下,也易使曲轴产生疲劳断裂。按要求飞轮摆差不能超过0.8mm。4 m+ x; }) Q& s- n) n, {8 \& l3 ^
(6)曲轴与飞轮的锥孔配合不符合技术要求。若两者之间贴合不是接触而形成线接触,则发动机工作时,飞轮就会松动,造成曲轴与飞轮之间的冲击,此时飞轮受到两个方向的冲击,将易使曲轴键槽两侧面很快出现裂纹,如继续使用,裂纹逐渐扩大,必将导致曲轴断裂。这种情况一般在单缸机中多见。' t$ g/ g6 ?8 q* a
' X/ t5 ~5 a. ?" x; r; R9 m1 g5 N* s' c! r) p
??2.装配问题- e% c. I3 q8 N$ }
??(1)轴承装配间隙过大或合金脱落,引起冲击载荷增大。当曲轴转动之后产生甩动现象,或机器发生飞车、捣缸、顶气门等,造成曲轴过度受力,也可导致曲轴断裂。
3 i j6 z* q& ^6 @) J, n$ ^??(2)曲轴换装了不符合要求的平衡块,或安装时错位以及曲轴磨修时采用偏心法,使曲轴半径超差,破坏了原来的平衡,曲轴产生较大的惯性力,使曲轴疲劳而断裂。
9 N" s9 k W0 G! A??(3)在装配轴承时,各曲轴主轴承紧度不一,使曲轴轴颈受力不均而造成曲轴断裂。
' d/ G! ?2 A6 n, w7 f ??(4)曲轴轴向间隙过大,运转时前后串动,在柴油机负荷工作时,曲轴臂受到端面的附加反击力,使应力集中而加速曲轴断裂。/ A7 q# U% i( K0 f$ `- E
2 p( o2 S2 d- h' C! g/ n; m! Y
/ K9 w- |6 v2 i5 e) L??3.使用不当9 f6 p! R3 g9 Z
??(1)运行中发生飞车、烧瓦、抱轴、瓦盖断裂、活塞顶气门等事故,导致曲轴断裂。8 c* I0 p3 |; p/ v
??(2)飞轮连接螺栓松动,运转时曲轴发生抖动而失去平衡,产生较大的惯性力,使曲轴疲劳,极易在其尾端断裂。9 t3 c: K6 H# s- A! n o
??(3)发动机润滑油道不畅通,使曲轴与轴瓦长时间处于摩擦状态,导致曲轴断裂。
4 }* z2 d. }4 A& |/ d+ E' n??(4)轴颈磨损超过使用极限,或表面裂纹划痕太深,导致断裂。
% r9 m9 R, H8 H??(5)长期处于各缸供油量不均的情况下运转,因而各缸爆发力的大小也不一致,从而使曲轴各轴颈受力不均,时间长了也可能引起曲轴断裂。
: B2 u" E- R3 _- L??(6)在曲轴修整过程中,对曲轴主轴颈与连杆颈的圆角加工不够重视,修理后的圆角往往是几何尺寸及粗糙度不符合技术要求,则易使曲轴圆角处产生较大的应力集中,尤其曲轴轴颈经几次磨修后,由于轴颈尺寸相应减小,更易断裂。
1 j5 P8 ~5 Y( x) d S3 S( G??(7)曲轴弯扭变形超差,使不平衡量大大超过允许值,由此引起的不平衡离心力,将导致轴承超载,并使发动机产生强烈的振动,使曲轴断裂。
5 \( \% H& `2 L8 G??(8)供油时间过早,在活塞未达到止点前,柴油便燃烧,使曲轴受到过大的冲击载荷,由于机车长时间在此情况下作业,使曲轴疲劳而产生断裂。+ S: q- g) Z# M* X& Y# E: S. Y4 d* e
??(9)使用操作不当。如拖拉机起步过猛或长期超负荷工作,曲轴受到过大的扭矩作用,或过大的冲击载荷,导致曲轴断裂。另外,由于操作不熟练,工作中油门控制不好,忽大忽小使发动机运转不平衡,曲轴受到较大的冲击载荷,长期在这种情况下工作,造成曲轴断裂。1 l9 `0 S; `# [2 q `
??(10)在使用中,不踏离合器踏板而猛烈紧急制动造成曲轴断裂。
# t, b& t/ b/ W% @ ; L; G% X9 h: f2 A
7 `# E( d! L$ }; u; ^
??三、曲轴断裂的预防措施# k1 C, |. D; b6 h7 I
??1.保证机加工的技术要求和使用中的合理性
6 |# m6 j1 a% a, }0 A3 L& ^??(1)首先保证材质符合技术要求,以避免曲轴在运行中所承载的载荷远远超过曲轴本身的疲劳极限而引起过载断裂。1 s8 i+ Z' F- h% t& F5 g5 V0 k
??(2)轴颈尺寸、圆角、光洁度、动平衡等机加工全尺寸,必须保证满足技术要求。
6 y+ O Y4 K) q# A2 l! ]; v??(3)在安装曲轴之前对其主要技术要求(如曲轴的连杆轴颈圆角、曲轴半径、曲轴飞轮组件的动平衡等)进行严格的检验,应符合标准规定。2 ]8 \; h% Z2 ^( m! p
??(4)曲轴与飞轮的锥孔的配合应符合技术要求,两者之间的贴合面在75%以上,以避免贴合面过小引起飞轮松动,造成曲轴与飞轮之间的冲击。3 N% }: {3 ]1 i$ e
??(5)各缸供油量(或点火)应均匀,并使供油提前或点火时间符合技术要求。
8 R7 o7 o+ \! R* k" e??(6)曲轴轴颈与轴瓦的间隙,应符合技术要求。间隙配合是为更好的转动和润滑,过渡配合和过盈配合都有可能使得轴与轴套之间摩擦系数过高和润滑油不能进入工作面。
0 p- K4 s6 ^1 N8 G1 } z??(7)按规定的顺序和扭力距紧固飞轮与曲轴的连按螺栓,并加以锁紧,以防松动。
$ O' R4 L" h. K??(8)避免发动机在超负荷条件下工作,并防止突爆的发生;机车重载时,应平稳起步,不可抬脚过快,遇到障碍物时,不要加大油门猛松离合器硬冲;机车行驶中,一般应先踏离合器脱档后再制动停车;正确控制油门,切勿忽大忽小。
- i* E) p% `& [3 D3 H1 k??(9)保持发动机润滑系统中油路畅通,润滑油充足。使润滑良好,以避免造成轴瓦与轴颈发生干摩擦。 u) o$ Z; x2 P
??(10)发动机大修时,应对曲轴进行磁力探伤检查,也可用浸油敲击法、锤击法,当曲颈表面有径向裂纹,或有较深的延至主轴肩圆角的轴向裂纹时,不易修复使用,应立即更换曲轴。4 U4 v! m+ l. p- |% s3 b6 t
" u; w% b1 x% t$ |# Q/ a+ V5 W: h
: G; h- C8 A" Q+ }& N* P) P- P4 i: p??2.改善曲轴的疲劳性能
- w9 H3 _, A+ y. O& R??改善曲轴的疲劳性能,是降低曲轴断裂的关键,圆角滚压是曲轴强化的非常有效的措施,同时它也是提升企业竞争力的核心技术。( v3 M& Z6 I+ g
??通过采用各种强化方法提高材料的强度,尤其是表面强度,在轴颈R角表面形成残余压应力,可使疲劳强度显著提高。此外,能修复曲轴上各种能引起应力集中的缺陷、刀痕、尖角、截面突变等造成的质量问题,从而提高曲轴的抗疲劳能力,像圆角滚压强化、氮化圆角强化、感应淬火圆角滚压强化等复合强化工艺是最有效的强化手段,即提高了曲轴的疲劳强度,又改善了曲轴表面的耐磨性。仅就圆角滚压来说,能使曲轴产生表面压应力,提高表面硬度,改善表面光洁度,结果提高整体的疲劳强度。现在各发动机曲轴生产厂家常用的是圆角沉割滚压强化,提高疲劳强度约80%以上,大幅度降低断轴率。
. _# y5 o8 M# p+ [5 i4 s??沉割滚压原理:在曲轴圆角处加工沉割槽,使用滚压技术,滚压轮在接触压力下沿着沟槽圆周方向移动,根据金属变形理论,零件表面在外力作用下,被滚压金属的原子间距离会暂时减小或晶粒间产生滑动,当外力达到一定数值时,被加工表面金属除产生弹性变形外,还形成塑性变形。由于塑性变形的产生,使零件被加工表面的形状、组织结构和物理性能都发生了变化,在圆角表层内产生一定残余压应力,使金属表面得到强化,提高了零件表层冷作硬化硬度,压平了微观不平度,降低了零件的表面粗糙度,被滚压金属表面的强度极限、屈服极限和疲劳极限都有提高。; o6 t4 A( z% `# j# c
??滚压效果与曲轴设计尺寸、材料强度、滚轮尺寸、滚压力、圈数等有关,在实际应用中,应根据产品的特点进行滚轮、滚压力、压入角、滚压圈数等的选择,力求能充分发挥出曲轴材料、圆角滚压的优势作用,提升产品的品质。
# G3 h( D- M; N6 @' ^2 m S 1 ` c1 ]6 @7 w3 A/ k! c
( c: l+ h( j" c4 p! ^/ [
??四、结语
0 m. \7 p& A2 F H) R??发动机曲轴工作过程中的断裂,是非常严重的失效事故。有材质、机加工、装配、使用、维护等多方面的原因,由此,分析断裂机理、规律,优化制造工艺方案、严格控制生产以及装配过程,合理的使用、定时保养维护以及更换,确保曲轴的质量要求和使用要求能满足发动机正常运行的需要,特别严禁在运行过程中的违规操作,尤其通过提升曲轴本身的疲劳性能,可显著地降低断轴率。
c& h+ p8 y: p7 L 发动机曲轴断裂原因 |